The benefits of edge computing for manufacturers
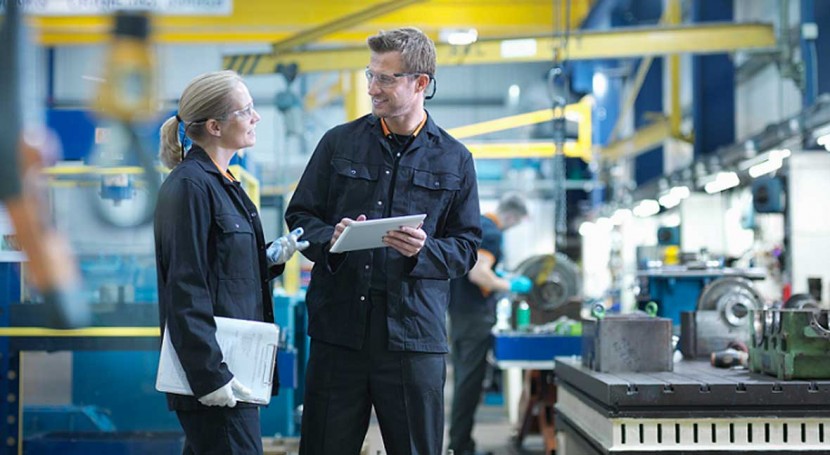
Guest post by Graham Immerman, VP of Marketing for MachineMetrics
The integration of edge hardware and edge computing within manufacturing facilities is set to disrupt industrial efforts in many ways. The ability to process and analyze data near a machine is incredibly valuable, especially in time-sensitive scenarios. Below we outline a variety of use cases and benefits that manufacturers can experience when leveraging the edge.
Predictive Maintenance
The ability for machines to analyze the data they produce allows for the integration of preventive maintenance business models in manufacturing. Here, assets within the shop floor will continuously create alert tickets to notify enterprise systems about underperforming components. These assets also create preemptive maintenance schedules that drastically reduce the possibility of unplanned machine downtime. The value-added propositions that come with a data driven predictive maintenance business model include:
– Reduced downtime
– Reduced maintenance cost
– Increased reliability and equipment efficiency
Energy Efficiency Management
In the United States, the industrial sector accounted for 32% of the energy consumption according to the US Energy Information Administration (EIA). This highlights the amount of energy that goes into manufacturing which affects the pricing of products. With edge computing, the consumption capacity of individual manufacturing equipment can be analyzed in real-time. Thus, providing a foundation for more efficient energy management policies. The benefits of this include:
– The ability to customize production modes and processes
– Lower energy consumption
– Reduced total manufacturing cost
Data-Driven Inventory Optimization
Edge computing makes access to data from individual components in a machine assembly possible. Analyzing the data from individual components introduces a preemptive approach to part replacement and provides guidance when stocking replacement part inventories. In more advanced scenarios, edge models can be developed to give manufacturing equipment the ability to request their own replacement parts before failure occurs. The benefits of this business model include:
– Reduced replacement costs
– Reduced unplanned downtime
– An automated spare part supply process
Developing New Business Models
Industry 4.0 business models all revolve around the use of data to enhance manufacturing processes. The model could either be a data-driven plant optimization model or a data-driven quality control model. These models will rely on the data edge hardware to provide a pathway for brownfield facilities to gradually implement smart manufacturing business models. The benefits of using edge computing to drive the development of business models include:
– A more efficient manufacturing process
– Enhanced quality control measure
– Increased product quality
Data as a Service
Equipment as a Service (EaaS) refers to the provision of data to users who require it to inform related processes. In terms of manufacturing, the data produced by edge computing can be sourced by manufacturers to develop new business models or fine-tune shop floor practices to increase revenue generation.
EaaS can be implemented in two different ways. They include providers of the equipment (machine builders and distributors) providing manufacturers with their curated data at no initial cost while collecting a percentage of the product or relational data its use produces. The other way EaaS functions involves manufacturers connecting equipment to centralized data sources or platforms to receive business insight.
What About the Cloud?
Edge computing will not replace cloud computing, though the two approaches can complement each other. Cloud computing is a more general-purpose platform for data collection, analytics, and historical reporting, but there are hundreds of use cases where reaction time is the key value of the IoT system, such as certain predictive maintenance events, where sending real-time data to the cloud prevents that analysis from happening quickly enough. Thus, by incorporating edge computing into their factory stack, companies can embrace a new frontier in manufacturing analytics, maximizing the potential of both approaches while minimizing their limitations.
About the author
Graham Immerman is VP of Marketing for MachineMetrics, Manufacturing’s First Industrial IoT Platform for Machines. Graham has quickly become an authority on digital transformation and the application of IIoT technology for the manufacturing industry. Graham spent his early career working on Madison Ave. at global and boutique marketing firms to help craft successful digital marketing strategies for brands like Adidas, Reebok, H&RBlock, and Starbucks. Find Graham on LinkedIn. MachineMetrics is also on Twitter and LinkedIn.
DISCLAIMER: Guest posts are submitted content. The views expressed in this blog are that of the author, and don’t necessarily reflect the views of Edge Industry Review (EdgeIR.com).
Article Topics
analytics | data | edge AI | IIoT | Industry 4.0 | MachineMetrics | predictive maintenance | sensors | Smart Factories
Comments