LanternEdge says data center-level capabilities now needed in harsh edge environments
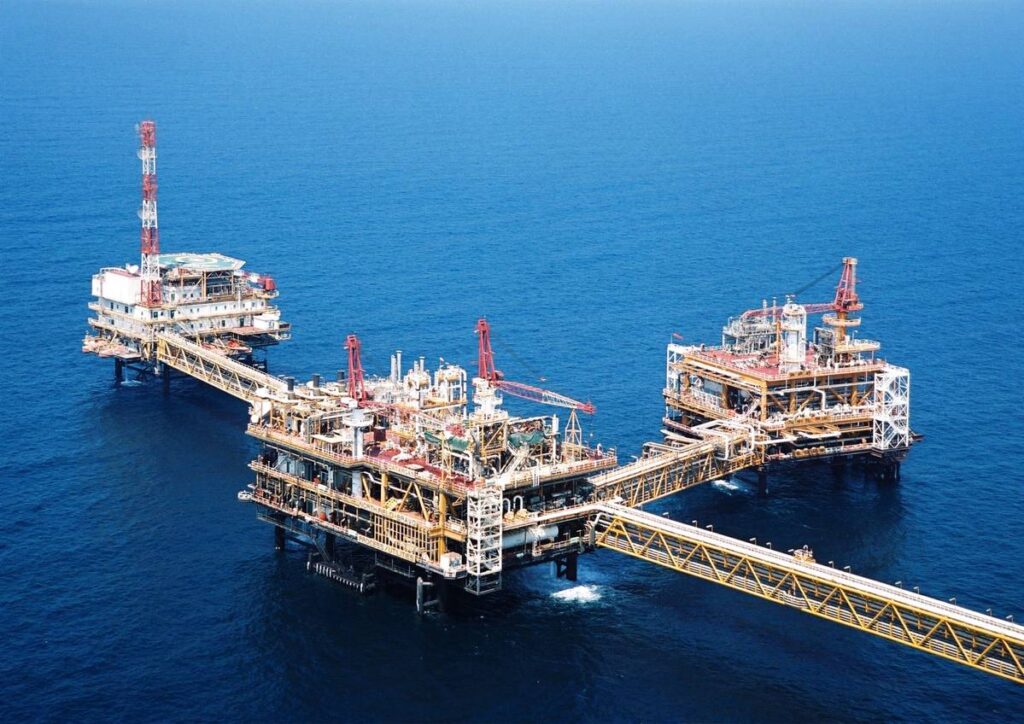
Industrial and manufacturing settings need reliable computing equipment that can handle a broad spectrum of applications. Singapore-based LanternEdge has been designing and manufacturing equipment for some of the most demanding environments in the oil and gas industry and is leveraging that experience to supply customers in what is referred to as the market for harsh and hazardous compute systems.
Harsh computing environments in industrial and manufacturing settings are typified by extreme temperatures, dust, vibration, water, and other physical or chemical elements found in manufacturing settings that can damage conventional computers. Hazardous computing is a step beyond, with environments such as chemical plants and oil platforms that require equipment to be explosion-protected, vibration and shock-resistant, pressure-resistant and corrosion-resistant.
Where products in these markets are typified by low power, older non-server class CPUs and motherboard designs, LanternEdge’s specialty is offering high-performance systems while still running reliably without fans. The company’s next-generation customizable HarshPro Servers, for instance, will offer the Intel Xeon D-2700 chips which were introduced by Intel in February. The chips allow the use of multiple virtual machines, operating systems and control systems, a key advantage in industrial applications where the hardware system might require the running of several operating systems. Another advantage: long-life reliability and the ability to run continuously, unlike non-server rated CPUs.
Just as important, the systems offer the flexibility to run software for hyperconverged systems such as the software from Sunlight.io that the company has verified against their systems. Hyperconvergence allows for scalability, security, high availability, efficient deployment, and ultimately lower costs, helping to optimize rugged edge computing environments.
Edge Industry Review recently spoke to Mark Mooney, COO of LanternEdge, along with Jake Berlocher, head of product, to talk about trends in the edge computing market, and the challenges of developing and managing hardware for harsh computing environments.
The following comments from the interview have been edited for length and clarity.
LanternEdge has a unique history, as hardware companies go. Can you tell us about how the company was founded and how it has evolved?
Mark Mooney (MM): LanternEdge initially started as a corporate innovation project in the upstream oil and gas industry. Those are extremely harsh and hazardous environments.
The project was around the safety of the workers in those environments [with] wearable devices and positioning and software related to data acquisition coming out of control systems in those environments.
We found it extremely difficult to find compute that suited our needs. Our solution utilized a modern software architecture based on microservices and containerization. That required server-class CPUs with a multi-core architecture. The machines needed to work as they do in the data center i.e. once computers are plugged in, no one needs to go near them – everything is accessible and administration can be done remotely. When you add on the requirement for the compute to operate reliably and survive in a harsh and hazardous environment, options don’t exist. That was the challenge that led to the founding of LanternEdge.
So you decided you needed to design your systems to support that worker safety application?
MM: We took the decision to build our own, right from the design of the motherboard up, supporting the type of CPUs we want, but also ensuring that the fundamentals of the complete package, were also designed for harsh and hazardous environments. This meant looking at the power consumption from the CPUs because one of the specific areas that we wanted was a completely fanless system with no moving parts within the system at all. To do that, the temperature from the power consumption and thermals of the design had to be very closely looked at.
There are differences between “harsh” and “hazardous” computing. Describe for us the dynamics of the different markets you address.
Jake Berlocher (JB): Hazardous areas are places like chemical plants, oil platforms, wastewater treatment plants, anywhere that you would commonly find a flammable atmosphere where you can have explosions. To deploy equipment into these hazardous areas, there are high regulatory limits; you have ratings like NRTL for North America, ATEX for Europe, and IECEx for the rest of the world.
There is a market for machines that are hazardous rated, but we see the market as quite limited. There are positive trends in the industry. On the process and control side, there is an emerging trend to move away from control systems based on proprietary hardware.
The Open Process Automation Group is being driven by many companies in process industries who are basically saying they want open interoperable hardware, and that it’s not sustainable to keep paying high prices. There’s a lot of interest in the industry.
MM: From our side, our target currently is the harsh environments, although the equipment is engineered for those hazardous environments. We will move with that market as it grows.
You are also working with customers to help them manage supply chain issues. Can you tell us about that?
MM: We do design here in Singapore. Our motherboards can be manufactured in plants across North America, Europe, and Asia. But to ensure supply chain and supply chain transparency, we will work with users and customers who really want to manufacture closer to where they’re deploying. We’re working with customers who maybe want to have manufacturing based in North America, for instance, because they can control the supply chain much easier. We’re quite willing to work with those teams who want to take the design and manufacture locally.
Some organizations need to have very clear transparency into where manufacturing has happened and sourcing for components and electronics that can be used. Being able to support that gives flexibility to companies who want to choose the equipment but also want to see exactly where the supply chain on the manufacturing chain has come from.
What do you see happening in the edge computing market this year? We have talked about standardized versus custom hardware and open-source software; what do you see are the key trends in the market?
MM: One key trend is the whole move in the software world towards a hyper-convergence of software, virtualization, and containerization of the software to support it. This will require the right underlying hardware and appropriate CPU.
The other trend is that customers have data center equipment, but also are maintaining and operating edge equipment and they want to treat it the same. They don’t want to have completely different operational procedures and software for their edge deployments, as they do for their data center deployments. Integrating into automation tools that people are using, such as Terraform and Ansible on bare metal as a service, provisioning it, and deploying the software onto it as if it was sitting anywhere in the world is something customers in our markets are seeking to do.
Cloud security analytics provider Devo Technology bags $100M in funding
Article Topics
chip | edge server | GPU | HCI | Industry 4.0 | Intel | IoT | LanternEdge | manufacturing | ruggedized | virtualization
Comments