LoRaWAN enables predictive maintenance at the Volvo Group factory in Lyon
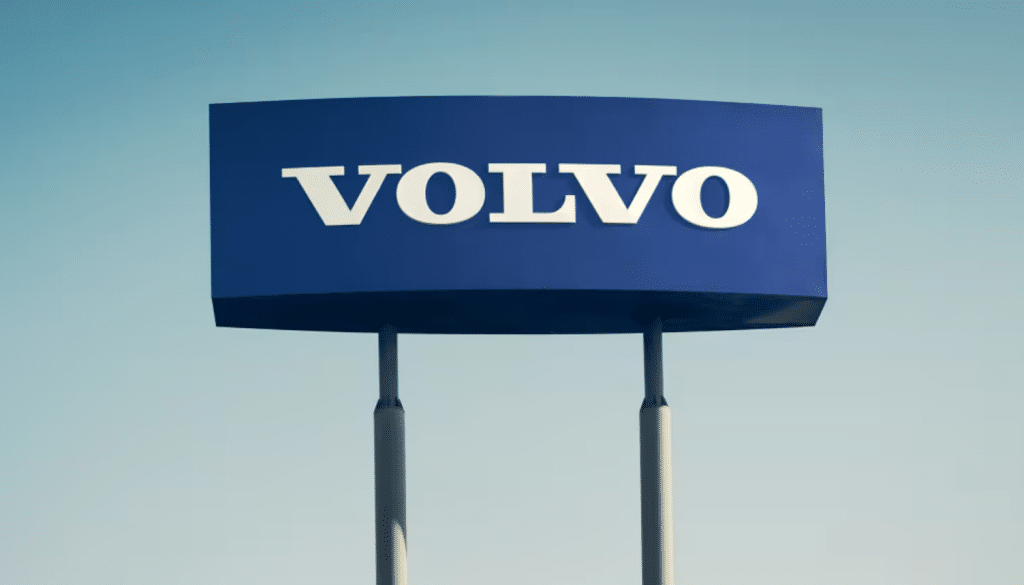
The Swedish multinational manufacturing company Volvo Group has implemented a new Internet of Things (IoT) network in its engine factory in Lyon, France, to monitor the health of its autonomous guided vehicles (AGVs).
The company says the AGVs enable more flexibility in Volvo Group’s engine manufacturing process compared to a traditional fixed production line. However, the AGVs rely on 24-volt batteries and unexpectedly stop when the voltage goes below 22 volts, resulting in a production loss of approximately two lost engines per week.
Volvo Group’s IoT team looked into wireless technology options to proactively monitor the health of its fleet of AGVs and avoid unexpected stops that disrupt its engine manufacturing process. However, the team found that the 2.4 gigahertz band was already being used for critical functions.
The team then evaluated LoRaWAN, a long-range wide area network protocol for connecting battery-powered internet of things devices. The Volvo Group says LoRaWAN is well-suited for manufacturing environments as it offers long-range resilience against interference and a secure and flexible network architecture.
Volvo Group’s IoT team installed LoRaWAN sensors on each of the AGVs to receive periodic data on the vehicles’ battery voltage levels. Thus, if an AGV’s battery voltage drops below 23 volts or fails, the maintenance team gets an alert via the LoRaWAN network, providing time to move the AGV to a charging point before it stops and disrupts the production line. The unit can also organize repairs for failed batteries.
To implement the LoRaWAN network, Volvo Group selected industrial-grade LoRa gateways from technology company Multitech. The gateways connect the LoRaWAN network directly to Volvo Group’s secure Ethernet network, avoiding dependence on cloud services.
The complete predictive maintenance system includes LoRaWAN sensors on each AGV, a private LoRaWAN network, and a maintenance platform running on PTC Thingworx with a mobile app and screens displaying real-time AGV status throughout the factory.
“Implementing a radio infrastructure in our factory was a challenge, and we wanted to have a LoRaWAN network connected directly to our secure Ethernet network to avoid any cloud dependence, says Julien Bertolini, the principal solution architect of IoT at Volvo Group Digital & IT. “So, we have selected a Multitech industrial grade LoRa Gateway, with some edge computing capabilities and robust cybersecurity features to successfully qualify it through a complete IT audit.”
In addition to monitoring AGV battery health, Volvo Group has added LoRaWAN sensors to its Lyon factory for other purposes, such as measuring temperature and humidity for painting processes to improve coating quality and detecting filter clogs via pressure difference sensors.
By implementing IoT technologies, the Volvo Group says it gained operational cost, speed and efficiency benefits.
Article Topics
Industry 4.0 | LoRaWAN | networking | predictive maintenance | Volvo Group
Comments